The rising production of man-made fiber (MMF) needs more dyeing units although the dyeing sector has been witnessing a dearth in investment due to shortage of gas over the last two years.
The dyeing segment cannot keep pace with the garment and spinning sectors’ growth as little investment was made in this important sector over the last two years.
Since the local garment exporters have targeted for more MMF based garment shipment, Bangladesh needs more and more dying units to gain more prices from the international retailers and brands.
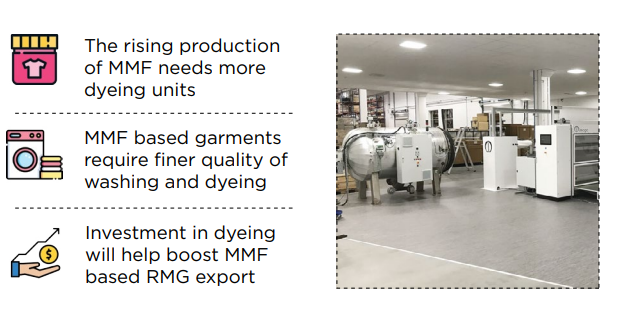
The MMF based garments require finer quality of washing and dyeing as the prices are also higher than the garment made from the cotton fibre.
The dyeing units consume a lot of gas with adequate pressure and it needs continuous heat for dyeing the fabrics. Because the dyeing units need at least 25 tonnes of boilers, gas generator and electricity which all need big investment.
Since there is a shortage of gas in the country, the entrepreneurs did not put money afresh in the sector over the last two years.
So, no new unit was set up in the dyeing sector, but only few entrepreneurs expanded their capacity to cater the local customers.
Currently, more than Tk30,000 crore is invested in the dyeing sector and more than 400 modern dyeing units are in operations now in the country.
Why dyeing is needed
Dyeing is a critical process to color fabrics and yarn for finished garment items. It involves a lot of technical people and expensive chemicals.
Two kinds of dyeing processes are required mainly — solid dyeing that means coloring fabrics and yarn dyeing for making fabrics.
However, the demand for local dyeing of fabrics has been rising rapidly to the local garment manufacturers because of shortening lead time by the international clothing retailers and brands.
For instance, previously the international retailers and brands allowed 90 to 120 days lead time, but now they have been allowing 45 to 60 days lead time due to fierce competition in the global apparel supply chain.
As a result, the garment makers like to use the local fabrics, rather than the imported fabrics for making the apparel.
Because, it needs at least 30 to 45 additional days if the garment is made from imported fabrics like from China and other countries.
So, the local garment suppliers like to use more local fabrics for making the garment and to supply to their international customers.
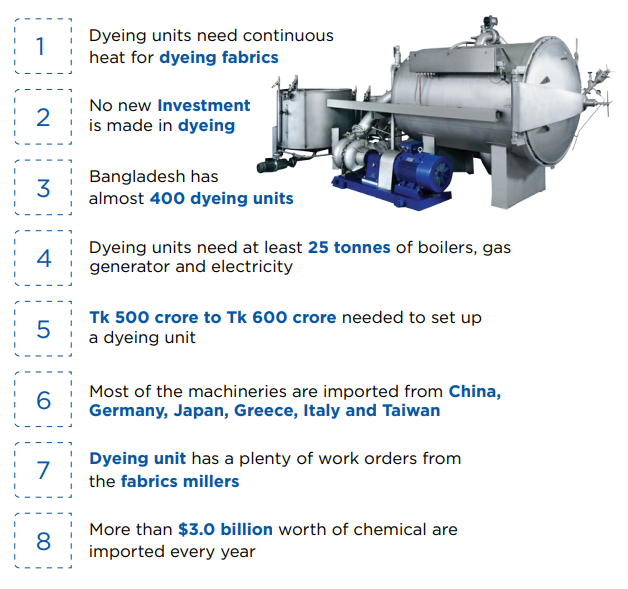
The current situation
The production capacity in the industrial units also fell to nearly 50 percent due to shortage of gas with adequate pressure.
Major industrial hubs like Gazipur, Maona, Bhaluka, Narsingdi, Savar, Narayanganj, Narsingdi and in Dhaka have been suffering from the shortage of gas supply over the last few years.
Currently, local spinners can supply nearly 90 percent fabrics and weavers can meet more than 40 percent of the demand for fabrics from garment manufacturers, who accounted for more than 85 per cent of Bangladesh’s export earnings of $55.50 billion in the last fiscal year.
Owing to the higher inflow of orders and the truncated lead time, many dyeing industries have already been transformed into composite units, which consist of the facilities and processes involved in turning textile raw materials into fabrics.
In Bangladesh, nearly 400 large dyeing units are capable of meeting the entire demand for knit and woven fabrics.
In such cases, the dyeing is very important segment as the garment makers need different kinds of fabrics with different dyes. However, the dyeing capacity has been lowered without any fresh investment and lower production capacity.
The dyeing units are running highest 60 percent capacity because of low gas pressure. However, the industry insiders are saying that there is a lot of work orders from the clothing makers.
What the industry people said
Md Rahat Ullah Rashed, head of Technical Support at the Taiwan Persotex Corporation & Taiwan TRS Ltd said the dyeing sector did not witness a massive investment over the last two years, but the entrepreneurs expanded their capacity as there were work orders from the local garment suppliers.
He also said the gas shortage was the main cause for not heavy investment in the dyeing segment. Rashed, however, said the machinery those the local millers use are expensive. But the dyeing units do not get adequate rate for dyeing from the customers.
The local dyers use the latest technologies for dyeing purposes, he said. Most of the machineries are imported from China, Germany, Japan, Greece, Italy and Taiwan, he said.
Bangladesh has also a handsome market for dyes chemicals as every year the local textile millers, dyeing millers and weavers import chemicals worth more than $3.0 billion to meet the growing demand of the local customers, Rashed also said.

The chemical consumption in the country’s dyeing sector has been increasing nearly 30 percent year on year.
Industry insiders said the old machinery needs to be replaced and many of the factories are getting less prices from the international clothing retailers and brands although they set up the most modern machineries in the mills.
Bangladeshi dyeing mill owners also need to set up dyes chemicals units so they need not to rely on foreign countries and companies for importing the dyes and chemicals for dyeing the textile and fabrics.
Monsoor Ahmed, Chief Executive Officer of Bangladesh Textile Mills Association (BTMA), said setting up a dyeing unit would cost Tk 200 crore to Tk 250 crore a few years ago but now it requires Tk 500 crore to Tk 600 crore.
The setting up of dyeing units is expensive as the state-of-the-art effluent treatment plant is needed for the dyeing sector, he said.
Also, BTMA President Mohammad Ali Khokon said with the inadequate supply of gas is not possible to set up a dyeing unit although there is a plenty of work orders from the fabrics millers.
Investing in such situation of gas supply, the entrepreneurs do not want to take risk and do not invest money in big amount, he said.
The supply of gas in the industrial units is needed to achieve the garment export target of $100 billion by 2030 might not be possible.