To create a sustainable apparel manufacturing supply chain, ensure more value addition in apparel export and attain $100-billion apparel shipment target by 2030, it is high time to take the primary textile sector to the next level.
The primary textile sector provides the raw materials and foundational processes necessary for garment production. By improving this sector’s capabilities in areas such as yarn production, fabric weaving, and dyeing, the overall quality and variety of materials available for garment manufacturing can be enhanced. This, in turn, enables garment manufacturers to add more value to their products through diverse fabric options, innovative designs, and improved quality control measures.
The value addition in Bangladesh’s apparel export is more than 60 per cent when local yarn and fabrics are used to make garments. However, the value addition is 30 per cent when yarn and fabrics are imported from foreign market, according to the Bangladesh Textile Mills Association (BTMA).
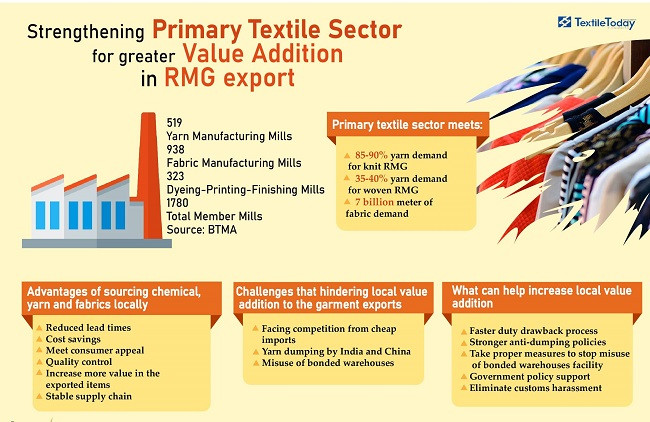
Apparel manufactures are adding value using local yarn, fabric and accessories. Now-a-day, many of them are using high end fabrics to make trendy attire analyzing consumer behavior. Value addition for fabrics refers to the systematic enhancement of fabric quality, aesthetics, functionality, and overall worth. This multifaceted process encompasses the application of diverse techniques, treatments, or processes aimed at elevating the visual appeal, performance, and utility of textiles.
Textile millers are diversifying their product ranges due to the rise on uses of local yarn and fabrics by the garment exporters. Producing yarn and fabrics require importing a huge amount of chemicals and dyestuffs. The more the garment manufacturers purchase the local fabrics, the more chemicals and dyestuffs are sold for washing and dyeing purposes. The more value addition yarn and fabric manufacturers will willing to ensure in their products, the more sustainable and specialty chemicals and dyestuffs will be used in fabric manufacturing.
Earlier, a report forecast that Bangladesh’s textile chemicals market will be $1.38 billion worth in 2024 which was $864 million in 2018. The demand of chemical is mostly meet by chemicals that are exported. The local production of chemicals is not sufficient to meet the demand, but reliance on imports should be reduced.
“Instead of importing chemicals from abroad, textile mills can save valuable foreign currency, reduce their inventory, and ease the lead time of garments export if they buy from local textile auxiliaries manufacturing companies,” recently in a conversation with Textile Today Md. Amanur Rahman, Managing Director of Dysin Group, said this.
“Reducing chemical and dyestuffs export and increasing uses of the locally produced chemical and dyestuffs can add more value in the overall apparel industry,” he added.
Using manmade fibre (MMF) is another way to add more value. Our exporters mostly dependent on exported MMF. As MMF production status is still insignificant in Bangladesh.
However, according to the recent data of Bangladesh Textile Mills Association (BTMA), around 85-90% yarn demand for knit RMG and 35-40% yarn demand for woven RMG are met by primary textile sector.
Local fabric demand i.e 7 billion meter of fabric are being produced locally to meet the domestic requirement and the yarn demand for handloom are also met by primary textile sector.
Current state of local value addition
Local value addition in the readymade garment (RMG) exports is increasing, indicating a shift towards higher-quality products and enhanced competitiveness in global markets. According to a report titled “Quarterly Report on RMG” released by Bangladesh Bank showed that the value addition in the RMG export increased by 11.59% over a one-year period.
The report said that the value addition in the RMG export was 54.38% in FY2021-22, which climbed to 65.97% in FY2022-23.
The central bank obtained export data from the Export Promotion Bureau (EPB) and sourced raw material import information from the Bangladesh Bank’s Foreign Exchange Operations Department, primarily gathered through back-to-back letters of credit.
The report said that in FY22, Bangladesh exported worth $46.99 billion RMG items for which the country imported raw materials like cotton, yarn, fabric, equipment and others worth $15.99 billion, meaning the net export of the RMG was $31.0 billion-dollar, accounting for 65.97% of value addition.
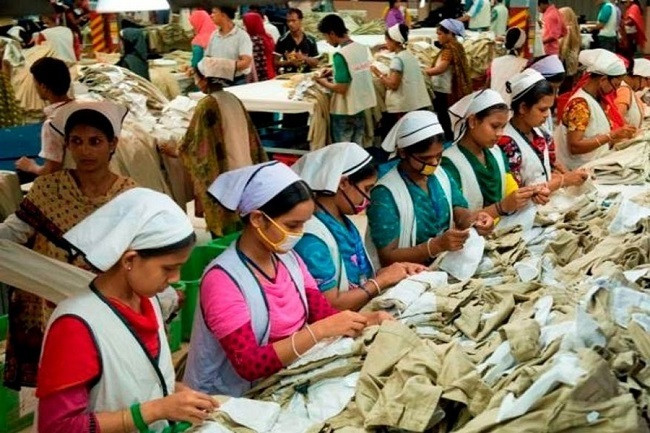
In FY22, Bangladesh exported RMG worth $42.61 billion. To produce that $19.44 billion was spent on importing raw materials. So, the export of net RMG was $23.17 billion and the value addition in apparel exports stood at 54.38% in that financial year.
Driving forces behind the value addition
Value addition is crucial for differentiating products in the market and meeting consumer demands. Incorporating value addition into the production of apparel products is also essential for creating a healthy supply chain, which is important for the long-term success and viability of the industry.
Now-a-day, international clothing retailers and brands are demanding a significantly shorter lead time to catch business in line with the recovery in the global supply chain from the severe fallouts of the pandemic and Russia-Ukraine war, so that garments exporters are relying more on local primary textile suppliers.
Global retailers and brands are eager for fresh fashion items, eyeing to expand sales seasons from six or eight to twelve due to heightened competition. Consequently, they demand swift delivery, often opting for costly air shipments instead of the traditional sea route.
Following such a change in the business behavior of international retailers and brands, the local garment suppliers, textile millers, weavers, spinners and knitters have also changed their production and procurement behavior to match up.
The local garment suppliers started procuring fabrics from local sources instead of imported fabrics to comply with demands for a shorter lead time.
Currently, international retailers and brands demand a lead time of 45 days to 60 days as opposed to the previous 90 days and 120 days for the delivery of goods.
Challenges ahead
Though Bangladesh is not a textile giant like India, Pakistan, or China, the primary textiles sector of the country always had a dominating presence in its apparel manufacturing sector. But the sector is suffering with many challenges, hindering value addition to the garment exports.
Some of the common challenges the sector is facing are raw material prices, increased production cost and gas shortage, the sector.
However, one of the major challenges in the Bangladesh textiles industry include an increase in competition as a result of cheap imports of yarn and fabrics from India, China, and Pakistan.
These nations are encouraged by their governments to engage in such trade practices. For instance, China offers exporters a cash return ranging from 15% to 20% when they sell goods to countries like Bangladesh.
The act of yarn-dumping, where India and China sell yarn at prices up to 30% lower than local production costs, severely hampers the ability of local textile industries to compete. Consequently, numerous textile companies find themselves forced out of the market due to an inability to maintain profitability.
This challenge is further exacerbated by local Ready-Made Garment (RMG) businesses importing raw materials via bonded warehouses, which are exempt from tariffs.
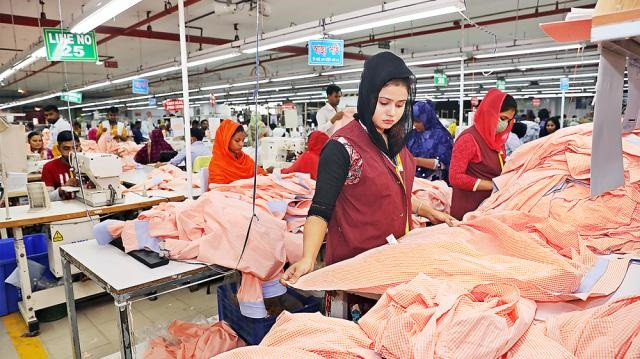
Md. Amanur Rahman pointed out the struggle primary textile sector is facing saying, “Duty drawback in many countries is automated. In Singapore, as exporter whatever GST you pay in the input, you will get refund of the input GST. And the process is fully automated. But in Bangladesh the process and regulation of duty drawback is very lengthy and clumsy. So that most of the industrialists of Bangladesh choose bond facility skipping duty drawback system. Because in bond facility they do not need to pay duty rather they can enjoy duty free import of input materials which puts the primary textile sector in jeopardy.”
Some companies unethically misusing the bonded warehouse facility affecting government revenue earning as well as impacting on primary textile sector. Customs has detected some irregularities and found that those products are often sold in the open market. Transparency and accountability should be ensure to eliminate the misuse of bonded warehouse facility.
Also, faster duty drawback process, stronger anti-dumping policies will need to be implemented by the government to protect the PTS. In addition to this, there must be greater regulation to prevent cases of smuggling of yarn and improper Utilization Declaration (UD) Certification in the case of RMG.
Apparel exporter should keep in mind that while they are thinking that low yarn prices as an advantage for the apparel exporting sector, it creates a problem of not being able to generate sufficient added value in the case of the final product and reduce net profit.