The denim manufacturing business stands at the crossroads between its iconic style and the urgent call for sustainability. While the demand for denim is rising daily, the environmental footprint of denim production is also growing accordingly. This, in turn, is the need of the hour not only for the planet but also for the longevity of the industry itself. Efficiency in denim washing increases and waste is minimized, hence reducing their impact on natural resources to a minimum.
This article looks at some of the innovative approaches and practices that are reordering the denim industry, transforming it into one that is much more eco-friendly, yet neither at the cost of quality nor style.
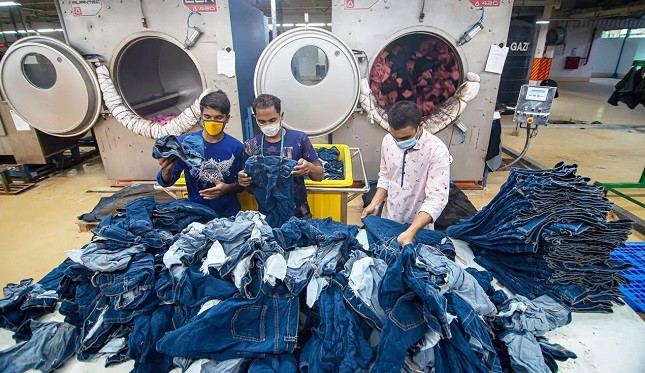
Smoothening out inefficiencies and waste are critical steps toward higher productivity and lower costs in manufacturing, service industries, and personal tasks. Following are strategies to improve efficiency and reduce wastage:
- Lean Principles
Muda (Waste Elimination): Identify and eliminate any process that creates no value. Seven traditional sources of wastes are over-production, waiting, transport, extra processing, inventory, motion, and defects.
Just-in-Time: Produce only what is needed in the quantity needed when it is needed to avoid wasteful unnecessary inventory and waste.
Kaizen/Continuous Improvement: Encourage a culture of continuous, incremental improvements at all levels within the organization.
- Process Optimization
Value Stream Mapping: Maps the whole process in order to find out the deadlocks, redundancy, and wastage of time. It will help in streamlining processes in order to avoid the useless steps.
Automation: Automate the time and repeated activities so that human errors are minimized to save the valuable time of yourself and offer good resources utilization.
Standard Operating Procedure: The main purpose of making a standardized procedure for any activity is to avoid the inefficiency in work due to different methods being applied.
- Resource Management
Energy Efficiency: Utilize energy-efficient equipment and make proper lighting also reduce time when machines are on idle conditions to waste less energy.
Waste of Material: Accurate measurement and design software ensures lessening the generation of wastes during production. Recycling material, where possible, also contributes to reduction in overall wastes.
Labour Deployment: Human resources shall be utilized for the tasks that are best suited for their skills and without over- or under-deployment of resources.
- Data-driven decision-making
Monitoring KPIs: Continuously monitor KPIs such as cycle times, production output, waste levels, and employee productivity to look out for processes inefficiencies.
Predictive Maintenance: Design systems to monitor equipment health so that breakdowns can be predicted and prevented in advance, thus reducing downtime and costly fixes.
- Employee Training and Involvement
Employee Skills Training: Trained employees on best practices, new tools, and means of efficiency will be more efficient. An educated staff will know how to identify and correct inefficiencies. Employee
Consulting: Engage employees in the efficiency process by encouraging them to suggest potential improvements.
- Waste Prevention Programs
Reduce, Reuse, and Recycle: Implement a policy that adopts reducing usage of materials, reusing as appropriate, and recycling.
Zero-Waste Goals: Have goals of minimizing or altogether eliminating wastes, especially in the food business or industries in manufacturing that over-utilize too much material.
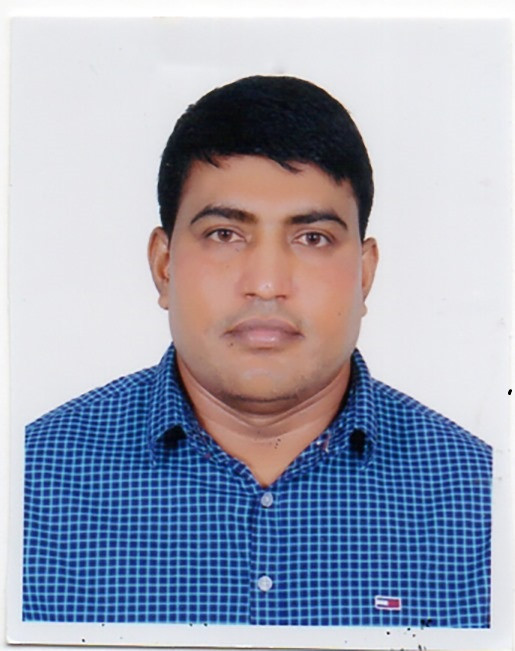
- Supply Chain Optimization
Cooperation with Suppliers: Work with suppliers in optimizing raw material deliveries, avoiding over-ordering, and wasting less due to over-packaging.
Logistics Management: Utilize proper forecasting models to ensure stock on hand at all times but avoid redundant inventory and losses from spoilage.
- Technology and Tools
AI and Machine Learning: Using AI in big data processing for inefficiency identification or more accurate demand forecasting to help in resource planning.
Digital Collaboration Tools: The usage of project management and/or communication software like Slack, Asana, and Trello makes it easier to coordinate everything within the team and minimizes probable delays.
With continuous process monitoring and optimization, new technologies, and a culture of continuous improvement, significant waste reduction and effectiveness can be achieved within an organization or by an individual.