Bangladesh’s spinning industry, a vital part of its textile and garment sector, has faced severe challenges over the past few years. As a crucial supplier to the country’s export-oriented garment industry, the survival of the spinning sector is essential for maintaining global competitiveness. The collapse of this industry would have serious repercussions, as garment manufacturers rely on locally sourced yarn to manage production costs and meet international lead times.
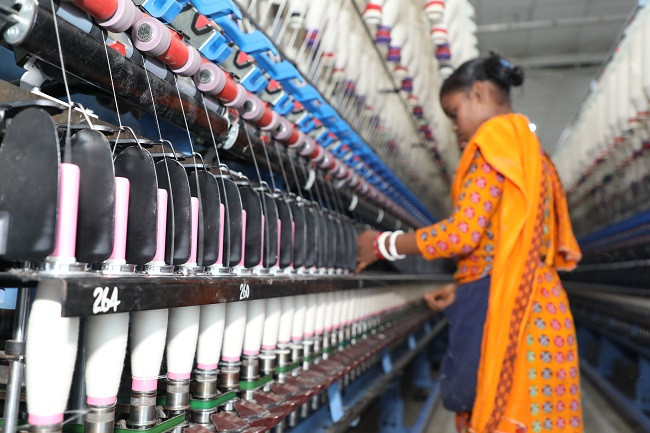
One key challenge for the garment industry is controlling the cost of yarn, which accounts for 60-70% of total production costs. Garment manufacturers prefer sourcing yarn locally to benefit from smaller inventories, quicker quality control responses, and easier payment terms. However, the significant price gap between local and international spinners pushes many Bangladeshi garment manufacturers to purchase yarn from abroad, weakening the domestic spinning sector.
The main reason for this price discrepancy is Bangladesh’s total dependence on imported cotton. Unlike major textile-producing countries like China, India, and Pakistan, which have access to locally grown cotton, Bangladeshi spinners rely entirely on imported raw materials. This dependence not only increases production costs but also limits the industry’s competitiveness globally. As a result, the spinning sector, instead of being a robust backward linkage industry, has become a financial liability.
Currency exchange rates further exacerbate the problem. While competitor countries buy cotton in their local currencies, Bangladeshi spinners must purchase cotton in foreign currencies, making it harder to predict profitability due to exchange rate fluctuations. Additionally, local spinners often have lower production efficiency and smaller output per spindle compared to international competitors, further straining the industry’s margins.
To overcome these challenges, the spinning industry needs to reduce its reliance on cotton by diversifying into blended yarn production. Blended yarns, such as cotton-polyester, cotton-viscose, and other synthetic fibers, could make up at least 50% of the industry’s production capacity. This shift would lower the industry’s overall production costs and enable it to compete more effectively with global players. Moreover, value-added yarns can support garment exporters in producing higher-quality, higher-priced products, enhancing Bangladesh’s reputation in the global market.
Government support is crucial for the survival of the spinning industry. One important step is imposing a 10-15% duty on imported yarn, which would help local spinners compete. Currently, garment exporters turn to Indian or Chinese yarn for its lower price for long lead-time orders. However, if the local spinning industry fails, Bangladeshi garment exporters will lose their ability to fulfill short lead-time orders, which are critical for maintaining competitiveness. At present, local spinners are incurring significant losses, and without government intervention, many spinning mills may be forced to shut down.
Upgrading technology is another essential step. Many Bangladeshi spinners still use outdated first-generation generators, which consume more gas than modern, fourth-generation generators. Upgrading these generators would reduce production costs by lowering gas consumption and making yarn production more efficient. Government funding or incentives could facilitate this much-needed technological upgrade.
In addition to technological improvements, Bangladesh must increase domestic cotton production. Currently, the country imports 97% of its cotton, requiring around 80-90 million bales annually. With the right policy support, Bangladesh could produce up to 20% of its cotton needs within the next five years. This would significantly reduce reliance on imports and lower the cost of raw materials for the spinning industry.
The government should urgently form a policy-making board involving all stakeholders in the spinning industry. This board would be responsible for developing long-term strategies to ensure the industry’s sustainability. Without a strong spinning sector, the garment export industry will struggle to survive, as it depends heavily on efficient and reliable backward linkages.