DyeMate is the new patented Tonello technology that revolutionizes and reinterprets the traditional indigo garment dyeing process, taking it to a new evolutionary stage and making it automatic and repeatable, efficient and sustainable.
Indigo dyeing with DyeMate
In traditional indigo dyeing, garments are dipped multiple times in a leuco (reduced) indigo solution and then exposed to air to oxidize and develop the characteristic blue color.
DyeMate has automated and made this entire process more efficient.
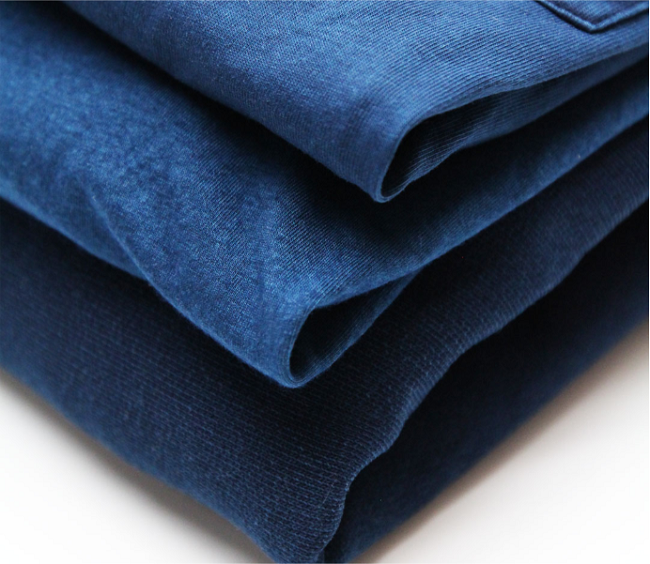
In the DyeMate process:
- A fully automated machine is used where the fabric or garments are loaded.
- Leuco indigo (the reduced form of indigo) is prepared, usually using hydrosulfite and caustic soda.
- Garments are dipped through short, controlled cycles in the indigo solution.
- Oxidation is carried out either by air exposure or oxygen injection, which develops the blue color.
- Each step is precisely monitored by process sensors, ensuring consistent results batch after batch.
Outcome: An authentic indigo look is achieved with less chemical usage, reduced water consumption, and shorter processing times.
Sulfur dyeing with DyeMate
Sulfur dyes are typically insoluble pigments and must be chemically reduced to become soluble for dyeing.
In the DyeMate process:
- Sulfur dyes are reduced using sodium sulfide or alternative reducing agents.
- Garments are dyed in this solution. (Traditionally, sulfur dyeing requires temperatures between 60–80°C, but DyeMate enables dyeing at room temperature or optimized lower temperatures.)
- Oxidation is then applied to reconvert the dyes into their insoluble form inside the fiber, fixing the color.
Advantages of DyeMate:
- Better dye penetration,
- Less streaking and uneven dyeing,
- Easy reproducibility.
Result: Deep shades (such as black, green, and red) with a denim-like appearance, developed consistently and efficiently.
Sulfur Essence – combined bath dyeing
Sulfur Essence is the most advanced process developed by DyeMate. Here, indigo and sulfur dyes are applied together in a single bath.
Traditional challenges:
- Indigo and sulfur dyes require different pH levels and reduction conditions.
- Compatibility issues between the two dye types.
DyeMate solution:
- Special dye formulations have been developed to allow both dyes to work together in a single bath.
- Digitally managed reduction and oxidation controls are used.
- An optimized chemical balance ensures no dye dominates the other.
Results:
- Discharge-like effects are achieved,
- Enhanced depth and texture are developed,
- The one-step process saves time, water, and energy.
Supporting technologies:
- Core 2.0, EGO, NoStone® — advanced finishing technologies fully compatible with DyeMate-dyed fabrics. (Example: NoStone® achieves abrasion without using real stones.)
- Laser marking compatibility — DyeMate dyes respond perfectly to laser effects, which is ideal for sustainable garment distressing.
Sustainability highlights:
- Lower water usage (single bath processing reduces the need for multiple baths),
- Lower temperatures (saving significant energy),
- Reduced chemical waste,
High reproducibility, minimizing the need for reprocessing.
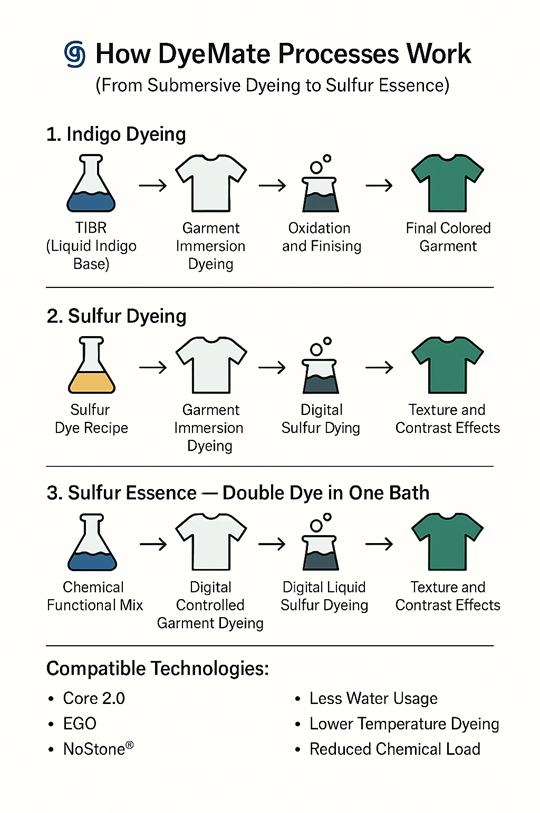
Dyeing recipes
- Indigo dyeing recipe (per liter of bath)
- Indigo Paste: 1.5–2.0 g/L
- Caustic Soda (NaOH): 1.0–1.5 g/L
- Sodium Hydrosulphite: 2.0–3.0 g/L
- Wetting Agent: 0.5 g/L
Procedure:
- Pre-wet garments.
- Prepare indigo bath with the above chemicals.
- Adjust pH to 11.5–12.0.
- Temperature: 50°C
- Dyeing time: 15–20 minutes
- Finish with H₂O₂ or air oxidation for color fixing.
- Sulfur dyeing recipe (per liter of bath)
- Sulfur Dye (Black/Olive/Green): 1.0–2.5 g/L
- Caustic Soda (NaOH): 1.5–2.0 g/L
- Sodium Hydrosulphite: 2.0–3.5 g/L
- Levelling Agent: 0.5 g/L
Procedure:
- Prepare the dye solution properly.
- Submerge garments and dye at 40–50°C.
- Dyeing time: 20–30 minutes.
- Oxidize and fix color.
- Sulfur essence (double dye recipe, per liter of bath)
- Indigo Paste: 1.0–1.5 g/L
- Sulfur Dye (Black/Olive): 1.5–2.0 g/L
- Caustic Soda (NaOH): 1.5 g/L
- Sodium Hydrosulphite: 2.5–3.0 g/L
- Wetting + Levelling Agent: 0.5 g/L
Procedure:
- Pre-wet garments and load into the machine.
- Prepare a combined dye bath.
- Pre-reduction and dyeing at 45–50°C for 15–20 minutes.
- Followed by oxidation using H₂O₂ or air.
- Finish with softener or acid wash and drying.
Challenges & solutions
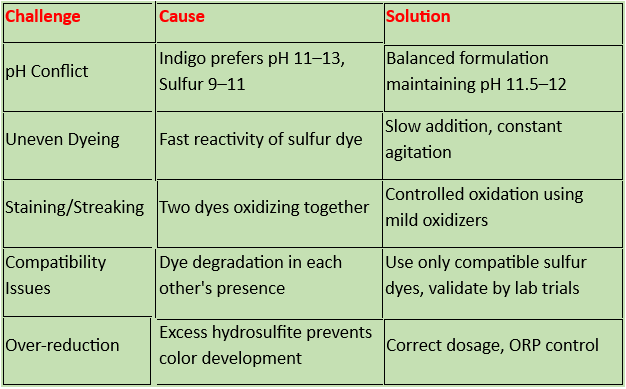
Machine suggestions for DyeMate process
- Fully automated rotary-drum type garment dyeing machine,
- Integrated pH & ORP sensors,
- Auto chemical dosing system,
- Air injection or vacuum oxidation stages.
Oxidation phase (post-dyeing step)
- Air dry garments or,
- Hydrogen Peroxide (1–2 g/L) + Acetic Acid bath for oxidation and fixing,
- Final wash with detergent and softener.
By combining precision, reproducibility, and environmental responsibility, DyeMate simplifies complex dyeing challenges—especially in denim manufacturing. Its compatibility with modern finishing technologies like laser and NoStone® ensures that it is not only efficient but also future-ready. As the textile industry continues to evolve, innovations like DyeMate will play a key role in meeting the growing demands for quality, consistency, and sustainability.