The global textile and apparel industries have faced monumental challenges. A potent mix of natural disasters and political unrest led to the shutdown of many factories across Bangladesh. As the local sector begins to rebound, tariffs spur additional threats, and the mix could cause significant waves across the industry if businesses fail to adapt.
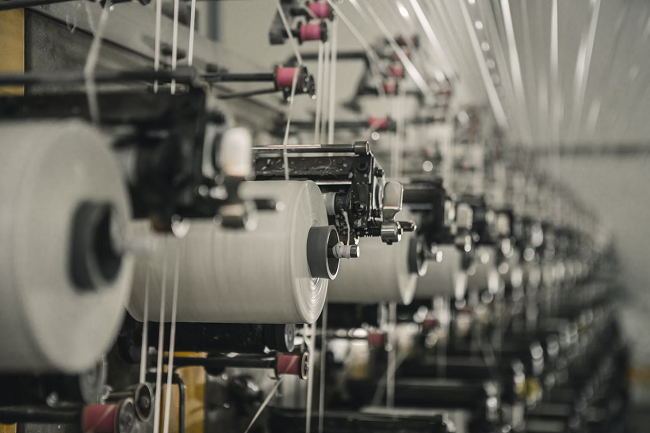
Inside recent textile factory closures and tariffs
The current crisis started in the summer of 2024 when students at Dhaka University began protesting the reinstatement of a controversial government jobs quota. Violence erupted, leading to increased unrest and lockdowns. Many factories had to close their doors as a result, causing textile production in the country to fall behind.
Not long after the protests, floods disrupted the nation’s supply and transport of cotton. The supply constraints and factory closures caused garment production to fall by 50% by late August.
By October 2024, most of Bangladesh’s garment factories had reopened, though political unrest continues today. Bangladeshi leaders say the industry has largely recovered from its shortfall, but workers still cite harsh conditions and low wages. The remaining controversy could cause production issues if it leads to additional disputes, layoffs or quit rates.
High tariffs from the U.S. exacerbate the issue. The Trump administration’s reciprocal tariff system implemented a 37% duty on Bangladeshi imports to the nation. While the president has since paused this tax, the lingering uncertainty and threat of high export costs still looms over Bangladesh’s textile sector.
How unrest in Bangladesh impacts global brands
While these events are all concentrated within Bangladesh, their impact stretches across the global apparel sector. Bangladesh is the world’s second-largest exporter of textiles, sending $10.2 billion worth of fabric and garments to the U.S. in 2022 alone. Consequently, disruptions in this nation significantly affect the world’s supply of materials and products.
Even though the nation’s factories are largely up and running again, the threat of lost productivity from further protests remains. Another pause or delay could leave companies relying on these sources unable to meet demand. This leads to lost sales and a diminished reputation among buyers, hampering future revenue.
Tariffs would also raise supply prices for U.S. clothing businesses with Bangladeshi sources. These higher costs force companies to make an uncomfortable choice between taking the impact themselves or passing it along to consumers, potentially resulting in lost customer loyalty and sales.
At the same time, overcorrection could create a bullwhip effect. Manufacturers may increase stocks to make up potential shortages or skirt tariffs before they take effect, but demand might fall before textiles reach store shelves. Such a scenario would leave businesses with additional losses from dead inventory.
How businesses can manage the disruption
The Bangladeshi supply situation is concerning, but it does not have to spell the end for textile and apparel businesses. Changes in both the short and long term can mitigate the impact of the current crisis while preventing similar situations in the future.
Seek alternative sources
The first move organizations should make is to look for alternate sources. Garment companies don’t have to cut ties with their partners in Bangladesh, but finding additional suppliers in other regions will help meet short-term demands while localized issues persist.
Businesses should prioritize reshoring, given tariff threats. In addition to avoiding import duties, a supplier can help fill last-minute demand gaps better if they’re geographically closer and can shorten shipment times. Regardless of location, distributed sourcing will likely entail higher upfront costs. However, these may be smaller than the expected losses if a company relies heavily enough on Bangladeshi sources that are currently unable to meet demand or absorb tariffs.
Streamline operations
Organizations should also seek to optimize their internal operations. Now that Bangladeshi factories are open again, shipments can resume, but tariff uncertainty warrants faster action. A faster internal workflow could mitigate that impact by increasing safety stocks and minimizing operational expenses to absorb the costs of import duties.
A few warehouse organization measures can produce significant results in this area. Shortening aisles leads to faster stocking timelines, and placing item drop-offs closer to storage racks can minimize picking times. While these changes may seem small, they can amount to significant overall savings.
Communicate expectations
Even with supplier and internal changes, delays and cost issues are still likely. Consequently, businesses should communicate these expected challenges to their downstream supply chain partners and customers.
In a 2024 study, 83% of surveyed buyers cited good customer service as the most important factor when making a purchasing decision. Notice the number one criterion isn’t shipping speed or price. Consumers value trust and transparency, so businesses are less likely to lose customers if they’re upfront about supply chain issues and tell potential buyers what they can expect and why.
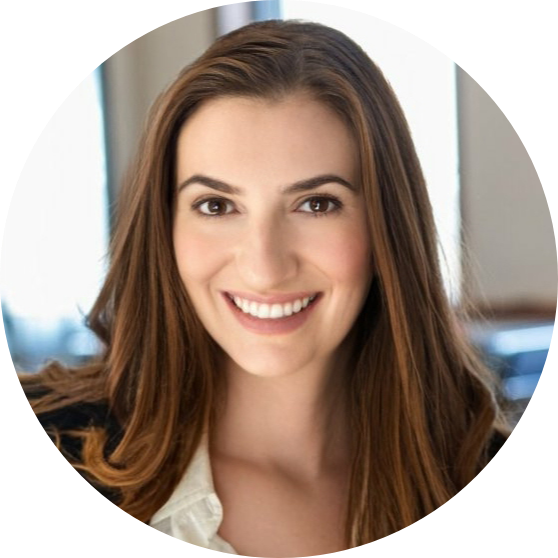
Consider broader supply chain restructuring
Finally, textile companies should look to the future of their supply chains. The current situation showcases the dangers of relying on a single location and highlights the fragility of logistics networks. Going against long-held lean principles in favor of resilience can help brands avoid similar crises down the road.
Distributed sourcing and reshoring are among the most critical changes. Organizations should also consider increasing safety stocks of high-demand items to mitigate any unavoidable shortages in an emergency. While these methods cost more upfront, they compensate through fewer lost sales.
Recent disruptions highlight the need for change
The current factory closures in Bangladesh won’t end the global textile industry, but they will disrupt it. Businesses adapting to the challenge should see it as a catalyst for positive change and take the opportunity to review how they can prevent and manage similar situations in the future.