Hanif Spinning Mills Ltd. in Bangladesh achieved a remarkable 10% increase in its ring spinning productivity, thanks to a 50% reduction in doffing time and an impressive 80% decrease in yarn breaks during restart. Rieter After Sales solutions do not only improve performance but contribute to the sustainability of spinning mills.
Mohammed Hanif, Managing Director, Hanif Spinning Mills Ltd (Fig.1) said, “The guiding arm refurbishment and doffer kit solution offered by Rieter helps us increase productivity by 10%. It improves the working performance of the machine by reducing the operators’ intervention significantly. We are planning to implement these conversions for the remaining 26 ring spinning machines.”
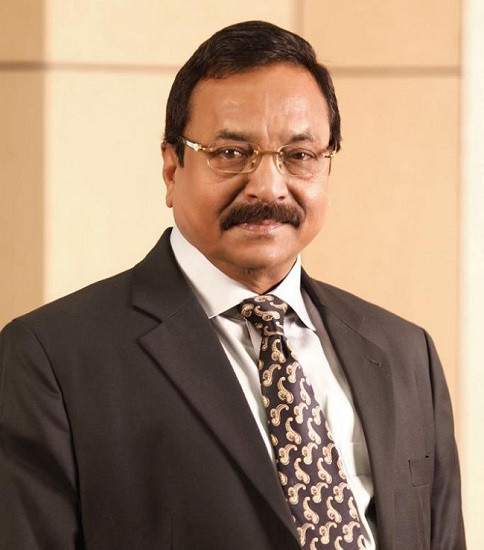
Hanif Spinning Mills Ltd. is renowned for its ability to consistently produce the best Ne 20 to 40 yarn in their segment in Bangladesh. The company has been running its ring spinning machines G 33 for over 20 years.
Due to the aging of the components in critical areas of drafting and doffing, the customer faced two major challenges that affected the machine’s performance and the operators’ efficiency, resulting in decreased production output. The first challenge was the load variation and random lifting of guiding arms which occurred due to key components that were worn out.
This led to quality inconsistency between spindles, undrafted roving, fiber lapping on top and bottom rollers and increased yarn breaks during running. To overcome this issue, the customer was forced to maintain a higher drafting load of above 2.6 bar.
A second challenge was the inefficient doffing cycle due to unwanted machine stoppages and manual intervention, resulting in reduced machine efficiency and an increase in restarting yarn breaks. The frequency of the doffer operation is higher due to the coarse yarn count being processed. Hence, the impact of the doffing cycle time is key to machine efficiency.
A solution with impact
The Rieter after sales team offered two solutions: the guiding arm refurbishment and the doffer maintenance kit. The guiding arm refurbishment consists of the pressure hose, top levers, pressure saddle and other technological components. This helps restore the original performance of the drafting system by ensuring a uniform load across the machine, resulting in stable drafting and consistent yarn quality.
The doffer maintenance kit consists of key doffer related components that help retain the doffing cycle time to its standard level of 180 seconds without any manual intervention.
Ensuring consistent yarn quality while increasing productivity
After the implementation of these maintenance kits on two machines (Fig.2), performance improved significantly. The guiding arm refurbishment enables load uniformity across the machine. Performance is ensured as all guiding arms are pressed evenly and the drafting pressure is maintained between the recommended 2.3 and 2.4 bar.
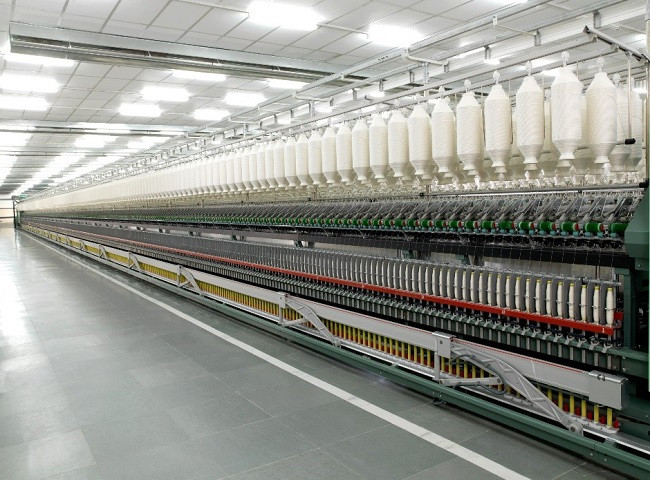
The doffer maintenance kit delivers the benefits of keeping doffing cycle time consistently low without any intermediate stoppages and always ensuring smooth doffing. To reduce the installation time, the doffer maintenance kit was delivered with pre-assembled parts. The implementation of these two solutions resulted in an increase of 10% in production due to the higher spindle speed and increased machine efficiency.
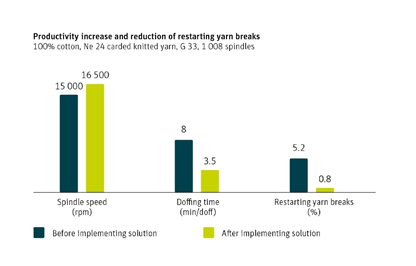
The spindle speed has been enhanced by 1 500 rpm because of the uniform drafting operations without any undrafted roving, without lapping and reduced restarting and running yarn breaks, which leads to raw material savings.
The doffing time has been reduced by around 50% and the restarting yarn breaks by around 80%, resulting in increased machine efficiency (Fig.3). Replacing worn-out and aged parts helped restore the original performance of the ring spinning machines.
This supports customers in optimizing the performance of their operations. It further contributes to the sustainability of spinning mills by extending the lifetime of Rieter machines.