
In the current landscape of the RMG manufacturing industry, profit margins typically hover around 7 per cent – 8 per cent per order, making it difficult for factories to support long-term sustainable operations. The industry’s narrow profit margins highlight the importance of efficiently covering expenses, including worker and management salaries, amidst various challenges such as the impact of Covid, the Russia-Ukraine war and a global economic slowdown. Operating under these conditions, factories strive to maintain functionality and financial stability.
As we look ahead, 2024 is believed to mark a resurgence for RMG factories, with the order scenario expected to return to normal. Despite this positive outlook, many factories are in the midst of expansion plans. However, the establishment of new factories involves arduous processes, consisting of at least two-year investment period that includes land acquisition, construction and order acquisition. This waiting period for orders to materialise poses a financial burden for both new entrants and established players, adding to the challenges faced by the industry during these demanding times.
The only answer is to increase efficiency and productivity in the manufacturing business to improve profit margins, while going for systematic expansion plans.
In the wake of productivity and efficiency improvement, Azim Group has opted for digital tools across its sewing floor and, as a result, its factories have realised 15 per cent increase in planning efficiencies and a 97 per cent faster turnaround in order confirmation. Prior to this, the capacity management and line planning teams in Azim Group lacked the pinpoint accuracy required to respond to the buyer’s latest changes. As a result, additional effort and regular reviews were needed from merchandising to ensure all teams had a unified approach to delivery. |
How factories are tackling efficiency challenges?
Rizvi Fashions – a leading RMG company with US $ 100 million turnover – has 65 sewing lines, while it is aiming to increase lines to 75-80 by 2025 in the already operational factories. This way, the company will add at least 350-525 sewing machines more. While the maximum number of machines will be producing boxers and underwear, some lines would be dedicated to products such as lingerie and other knitted items.
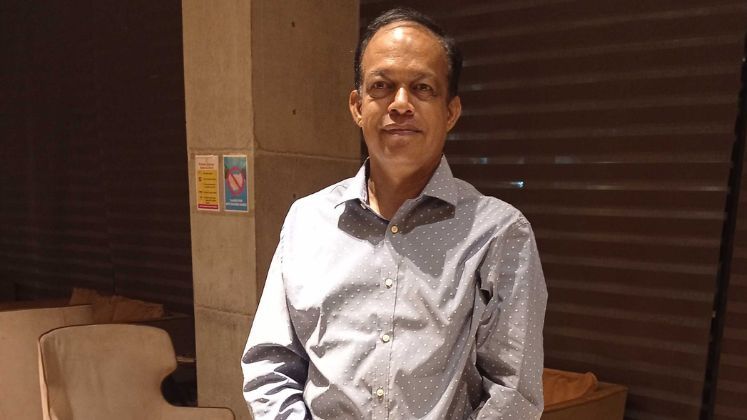
Shakil Rizvi, MD, Rizvi Fashions, mentioned the need to improve the efficiency of management personnel in his factories to achieve targets, as the industry has traditionally focused on worker-level efficiency but missed out on increasing management-level efficiency.
“Measuring senior and top management performance and decision-making criteria is an area of improvement as they are the ones who are running the show,” shared Shakil, adding that the company has opted for automation in its sewing units to track the line and floor efficiency and has seen positive initial results. “2-3 per cent efficiency increment is what we have witnessed on sewing lines through our initial investment and we will accelerate these tech-driven efforts,” averred Shakil.
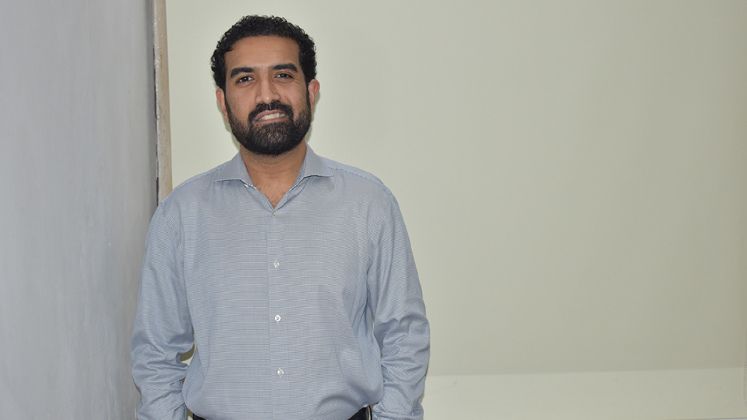
Endorsing the need for improving productivity and efficiency, Farhan Azim, Managing Director, Azim Group explained that in a highly competitive market, where a few cents can make or break a deal, the factories need to minimise costs to offer the best price to buyers which can effectively be done by increasing efficiency of workers on the production floor.
“A large portion of our overhead is worker salary. Hence, the logical step forward was to enhance the capacity of our workers so that we do not have to rely on redundant recruitment to increase capacity. Our highly proficient Industrial Engineering (IE) team provides extensive training to our production team to help them develop their capacities. As a result, our factories are performing at the highest levels of efficiency than ever before,” mentioned Farhan.
Further, in the wake of productivity and efficiency improvement, Azim Group has opted for digital tools across its sewing floor and, as a result, its factories have realised 15 per cent increase in planning efficiencies and a 97 per cent faster turnaround in order confirmation. Prior to this, the capacity management and line planning teams in Azim Group lacked the pinpoint accuracy required to respond to the buyer’s latest changes. As a result, additional effort and regular reviews were needed from merchandising to ensure all teams have a unified approach to delivery.
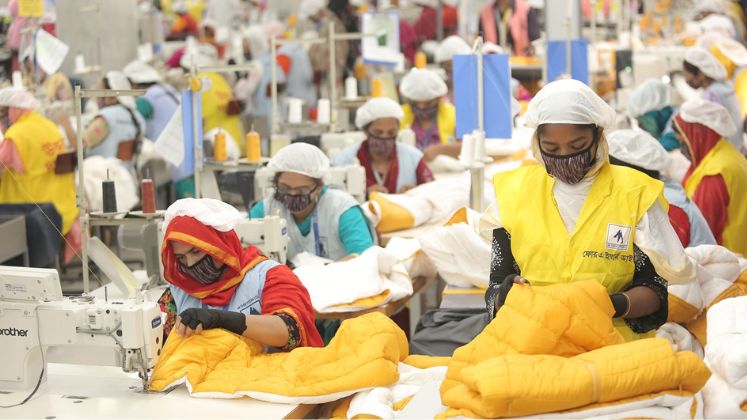
With minutes-based load versus capacity monitoring being accurately established on true actual line plans, Farhan believes that there are improvements across major KPI parameters including factory efficiency, planning efficiency, on-time-delivery and on-time T&A completion.
All departments are now using technology to create accurate, real-time reports and daily activity priorities, including KPIs. As a result, Azim Group has saved nearly six person days per month in time efficiencies – a 68 per cent time-saving in report generation.
Factory efficiency has consequently improved by 7 per cent; while Cut-to-Order, Ship-to-Order and Cut-to-Ship efficiencies have also improved by 0.37 per cent, 0.89 per cent and 1.36 per cent respectively.
The race for increasing visibility and efficiency across RMG industry in Bangladesh – especially the big groups – seems to be cracking success code amidst rising labour wages in the country. HAMS Group – that employs 12,000 workers across its factories – has also envisioned its factories to be completely driven by data in the near future to keep efficiencies on the highest side!
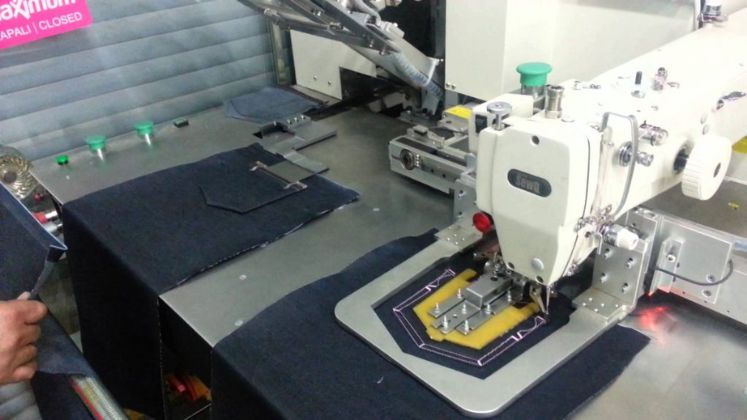
Shaifur Rahman, Senior Director, HAMS Group, commented that the group always needed to optimise efficiencies, while maintaining enhanced customer service by delivering smaller and increasingly complex orders on time. The group realised post-Covid that traditional ways will not be working out in the future and hence they needed to find solutions to important information siloed in different places across the business which drastically hampered the group’s productivity and efficiency in its RMG division.
“We have improved our efficiencies by 7 per cent after we went digital on our sewing floor recently,” commented Shaifur.
Even Norban Group – a vertically integrated knit-composite group – has stepped up digitalisation of its factories to better align Time and Action (T&A) priorities, connect more accurate planning and forecasting data, improve OTDP (On-Time Delivery Performance) and eliminate unnecessary firefighting across the business.
Shafiqul Alom Sumon, Director (Marketing and Merchandising), Norban Group, commented, “Our decision is to digitalise our operations by quickly identifying bottlenecks, reducing firefighting and providing the essential KPI monitoring and visibility we need to keep the business moving forward.”
The adoption of cutting-edge technology like advanced MES has yielded several benefits for the country’s promisingly growing apparel manufacturing company Dressmen Ltd.
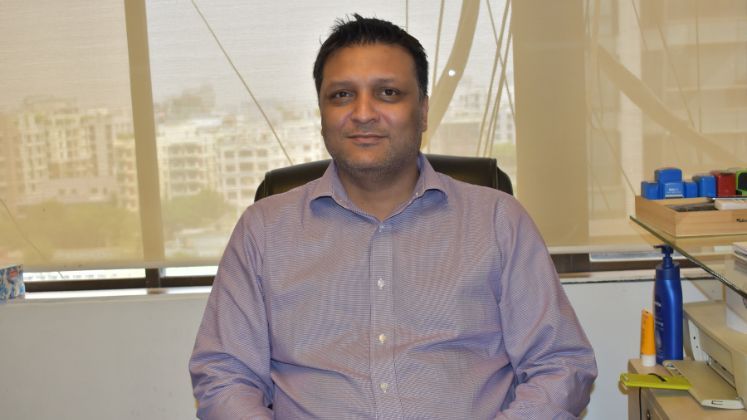
According to Maashed Rumman Abdullah, Director, Dressmen, it has heightened awareness amongst production floor personnel, fostering a culture of accountability. Moreover, the streamlined processes and enhanced data management facilitated by MES have enabled a 30 per cent reduction in middle management, resulting in substantial cost savings. Additionally, the company has experienced a 4 per cent – 5 per cent increase in efficiency, enhancing its overall productivity – that’s a much-needed factor that buyers in today’s time consider while placing orders.
“Buyers today look at how sustainable and productive are you! Nobody is going to pay for non-productivity and non-compliant processes, which is why we are focusing on both these areas strongly,” mentioned Maashed.